A 26 per cent jump from the previous year, the surge is expected to continue during the next phase of the wedding season, from mid-January to July, dates determined by their auspiciousness in the Hindu calendar.
In preparation, families often travel to one of a number of “sari clusters” across India, to pick up exclusive pieces, spending hundreds of thousands of rupees on brocade-rich Banarasi saris in Varanasi, Uttar Pradesh; on double-ikat Patola saris in Patan, Gujarat state; or on pure-silk Kanjeevaram saris in Tamil Nadu.
5,000 years of the sari, still at the forefront of fashion
5,000 years of the sari, still at the forefront of fashion
Paithan, on the banks of the Godavari river, in Maharashtra state, is synonymous with the opulent Paithani, a silk sari known for its rich, lustrous colours, floral and bird-inspired motifs and intricately embroidered gold or silver borders.
The gold-and-silk Paithani, also known as dev vastra (“fabric of god”), was popular in the 18th century, under the patronage of the Peshwas, the de facto leaders of the Maratha empire.
“The Paithani holds a deep cultural significance, symbolising prosperity, tradition and the essence of Marathi heritage,” says designer Gaurang Shah, who is considered an authority on the sari.
“It’s not just about the lavish attire; it’s a nod to the rich legacy and timeless elegance of every Marathi wedding.”
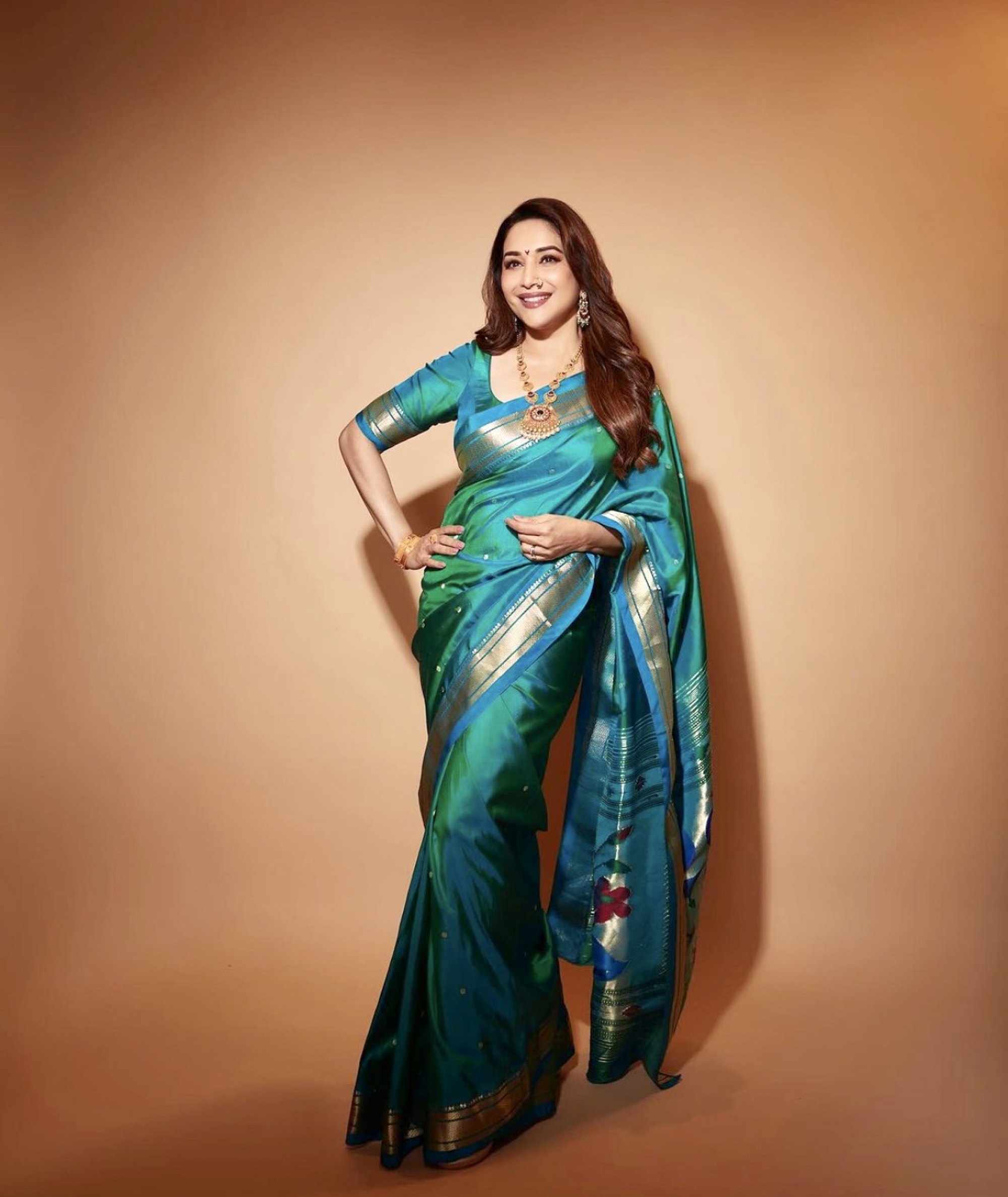
No doubt in agreement is Bollywood actress Madhuri Dixit, who recently donned a green Paithani sari replete with golden zari (thread) work for an awards ceremony.
The mass production of the Paithani has in recent times moved to Yeola, 135km (84 miles) northwest of Paithan, but weavers at the Paithani Silk Weaving Centre – which was established in 1984 in central Aurangabad, a city 50km to the north of Paithan – are preserving the traditional art form, showcasing the varieties, giving demonstrations and providing visitors with the chance to buy an authentic sari.
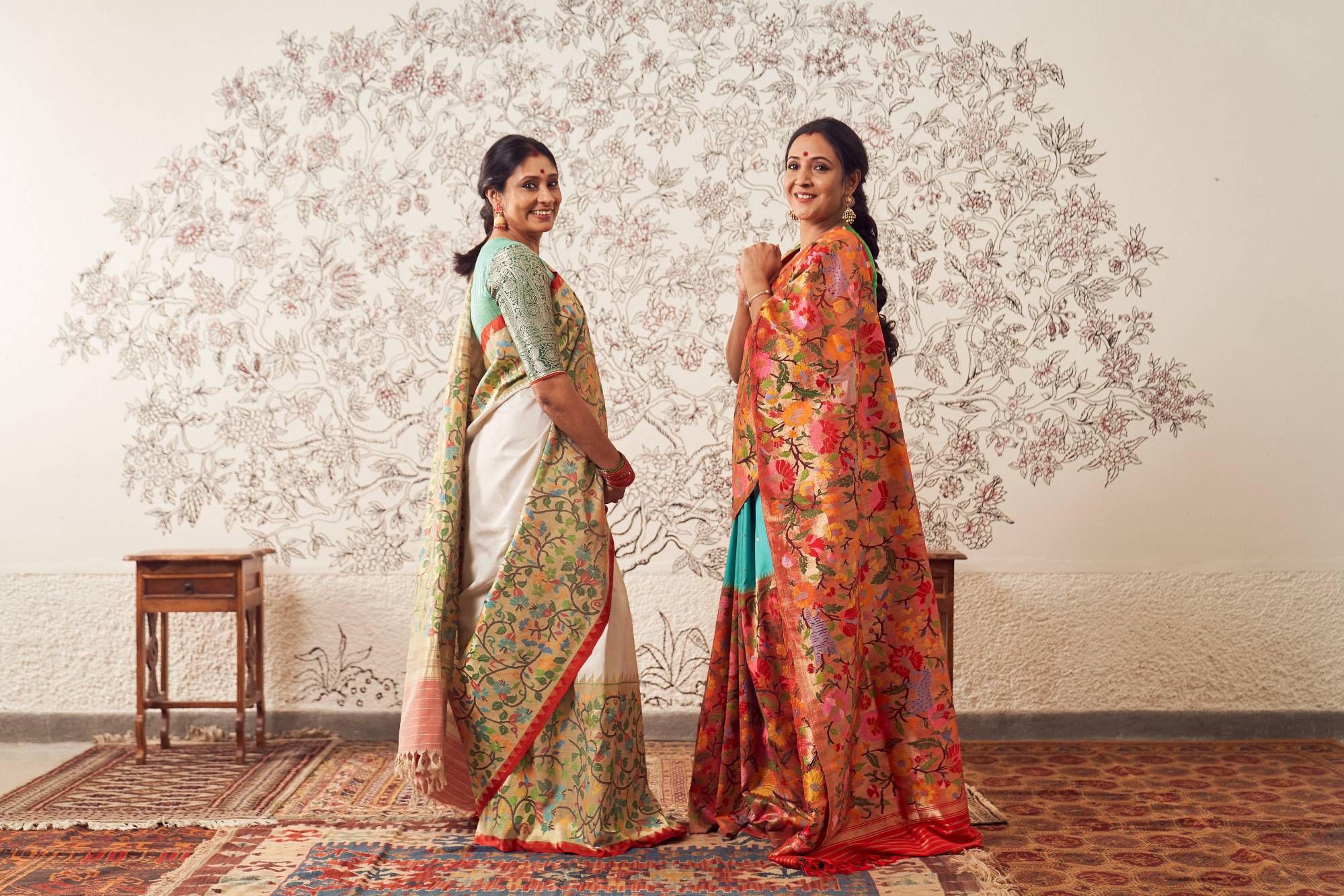
“A typical Paithani comprises the body [anga], decorative edge [padar] and borders [zari kath],” says Shantilal Bhandge, an 80-year-old National Award-winning weaver at the Paithani Silk Weaving Centre who has been practising his craft since he was 15.
“The padar is the most intricate and time-consuming part and could take between two weeks and six months, depending on the detailing.”
The walls at the centre are bare but the space takes on the richness of the craft. On a pair of traditional wooden handlooms, workers combine strands of mulberry silk with golden and silver zari to create the gorgeous weave. A genuine 5.5-metre (18ft) Paithani sari needs about 500 grams (1.1 pounds) of silk thread and 250 grams of zari thread, a weaver tells me.
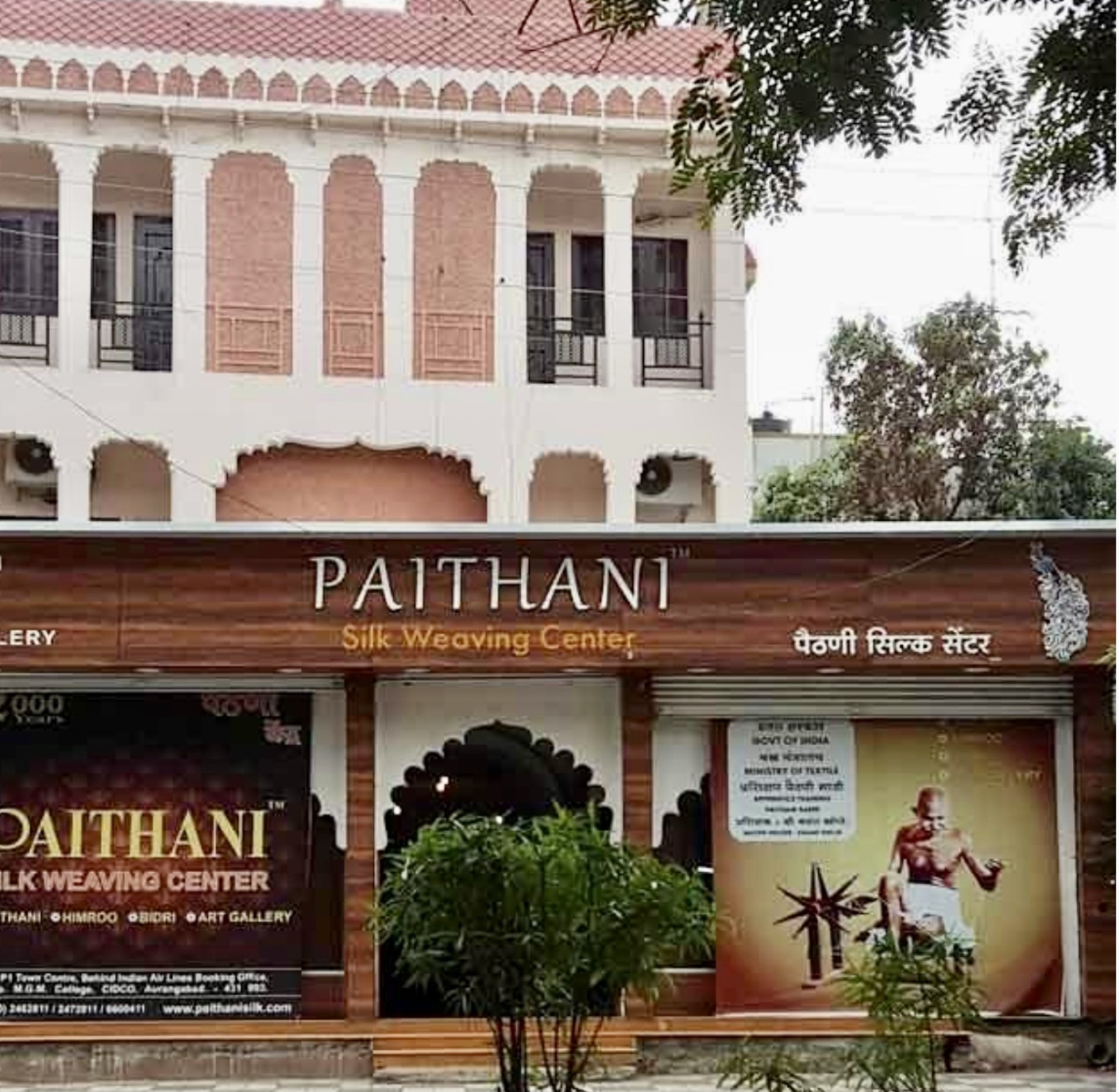
“[Tourists, buyers and students] need to see the handwoven item, not power loom Paithanis, which can be manufactured in about six hours,” says Bhandge, whose two sons own a showroom in Yeola.
In Gujarat, bridal parties head for Patan, to buy Patola saris, considered the “ultimate manifestation of weaving perfection”, according to Shah.
The history of the Patola can be traced back to the 12th century, when a king of the Solanki dynasty invited 700 weaver families from Jalna, Maharashtra, to settle in Patan and weave their magic.
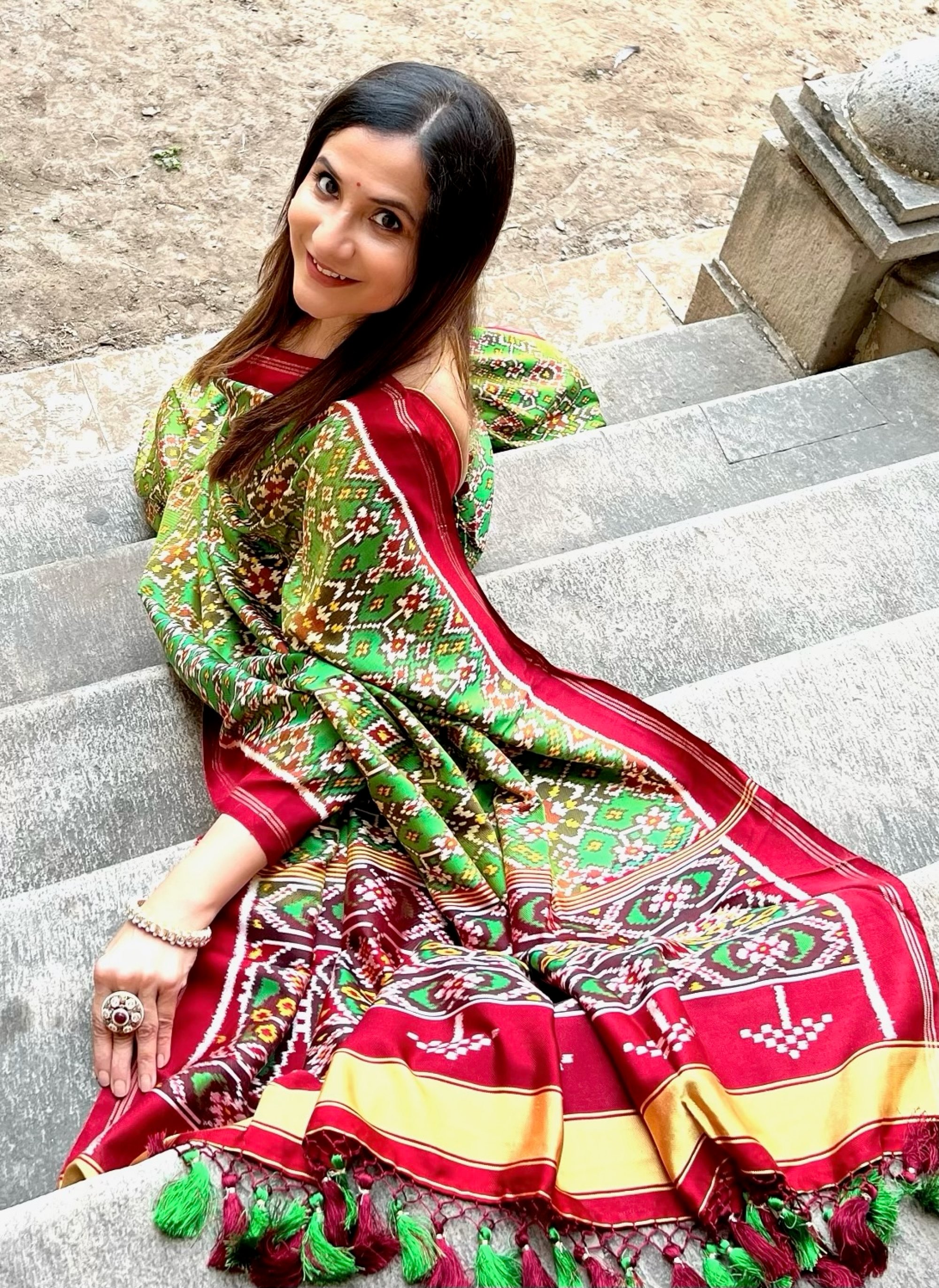
Shah, who is credited by celebrities and designers with having led the revival of the Patola, says its essence lies in the “intricate double-ikat technique”, the only type of sari produced with fabric that has been dyed using this method.
“It can take six months to one year to make one sari due to the long process of dyeing each strand separately before weaving,” says Savan Salvi, a member of the 38th generation of a family that has been weaving the Patola for nine centuries.
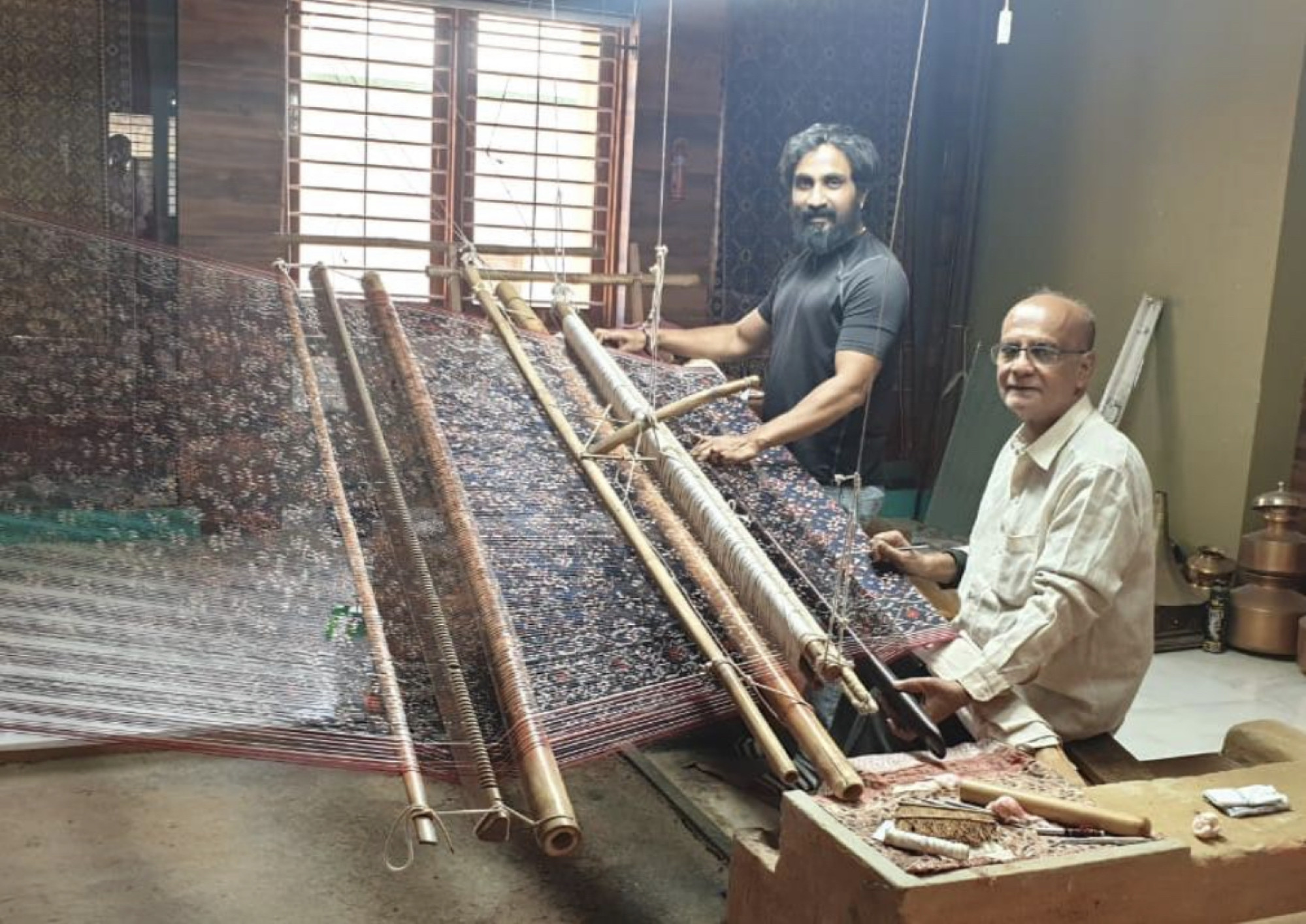
Rohit Salvi, the head of the National Award-winning family, says the price of an authentic Patola sari starts at 150,000 rupees on account of the extensive labour required, the resist-dyeing process and the use of vegetable dye.
However, such a sari “can last centuries, and is often passed on in the family like an heirloom”, he says.
Patola saris are typically made with red, maroon, green, yellow, white and black dyes, and the designs are based on traditional floral, animal, bird and geometric patterns. A genuine specimen weighs no more than 500 grams.
How Chinese influence shaped the Parsee gara
How Chinese influence shaped the Parsee gara
At the three-storey, 3,000 sq ft (280 square metre) Patan Patola Heritage Museum, run by the Salvis, a large loom stands in the centre of the main hall and draws the attention of visitors. It is used to show how silk threads come together to create the textile.
Elsewhere, wooden shelves and cabinets house the family’s treasures: Patola saris wrapped in muslin; old vegetable dyes; a 200-year-old red Patola frock made for a girl; old looms; and photos of celebrities wearing the saris.
Double-ikat textiles from Thailand and Indonesia are on display along with single-ikat examples from elsewhere in India, but pride of place is given to the Shikarbhat sari.
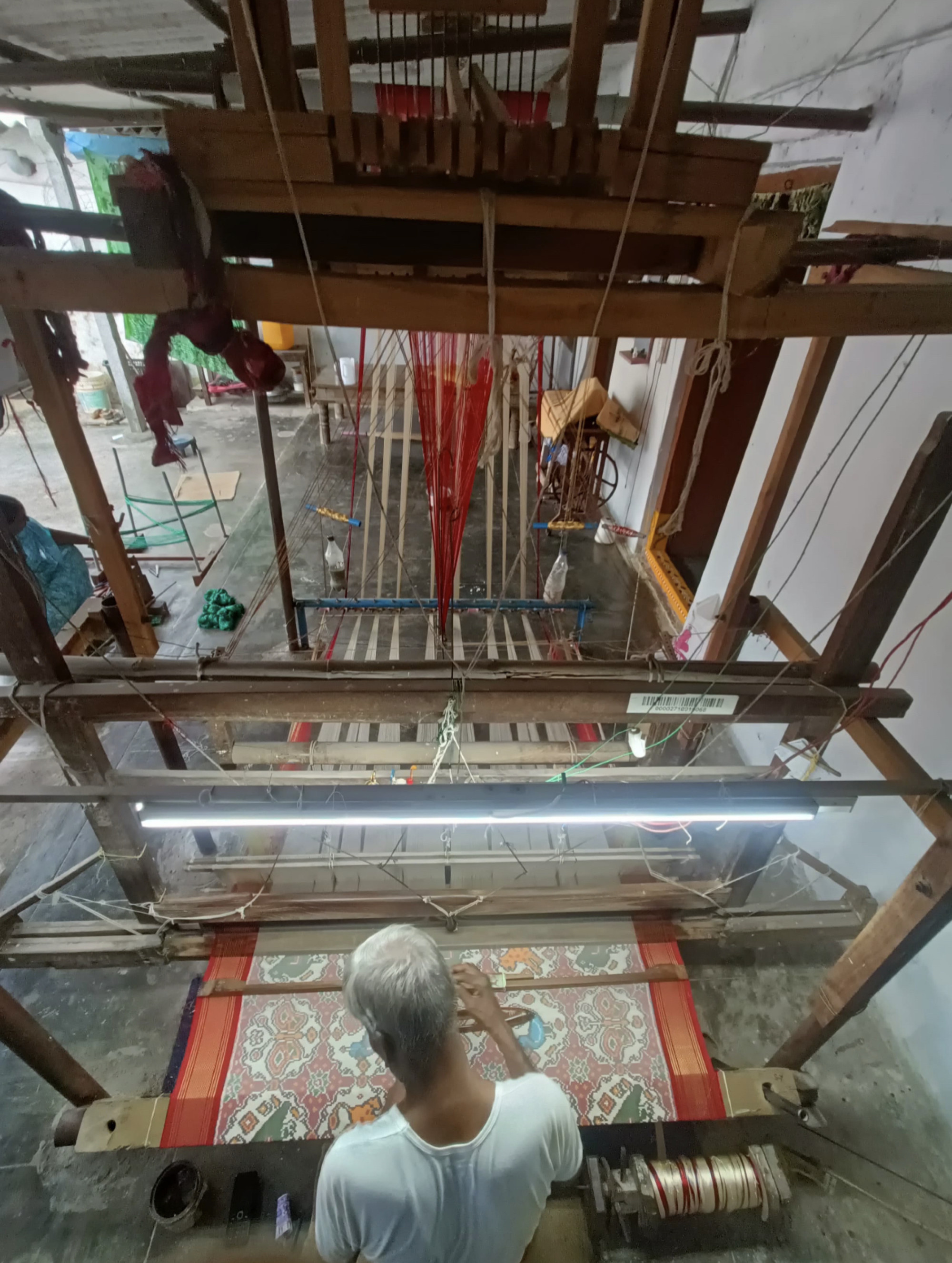
A recreation of a century-old item, it took three years to make and was completed in 2003, the red Patola garment decorated with the representation of a king’s procession, complete with a ceremonial elephant.
From Patan, I head to Pochampally, a small craft village in the southern state of Telangana. They may be separated by more than 1,300km, but the two places are bound by the ikat.
On the outskirts of Hyderabad, Pochampally is home to more than 10,000 weaving families, who have used the same looms, techniques and patterns for centuries.
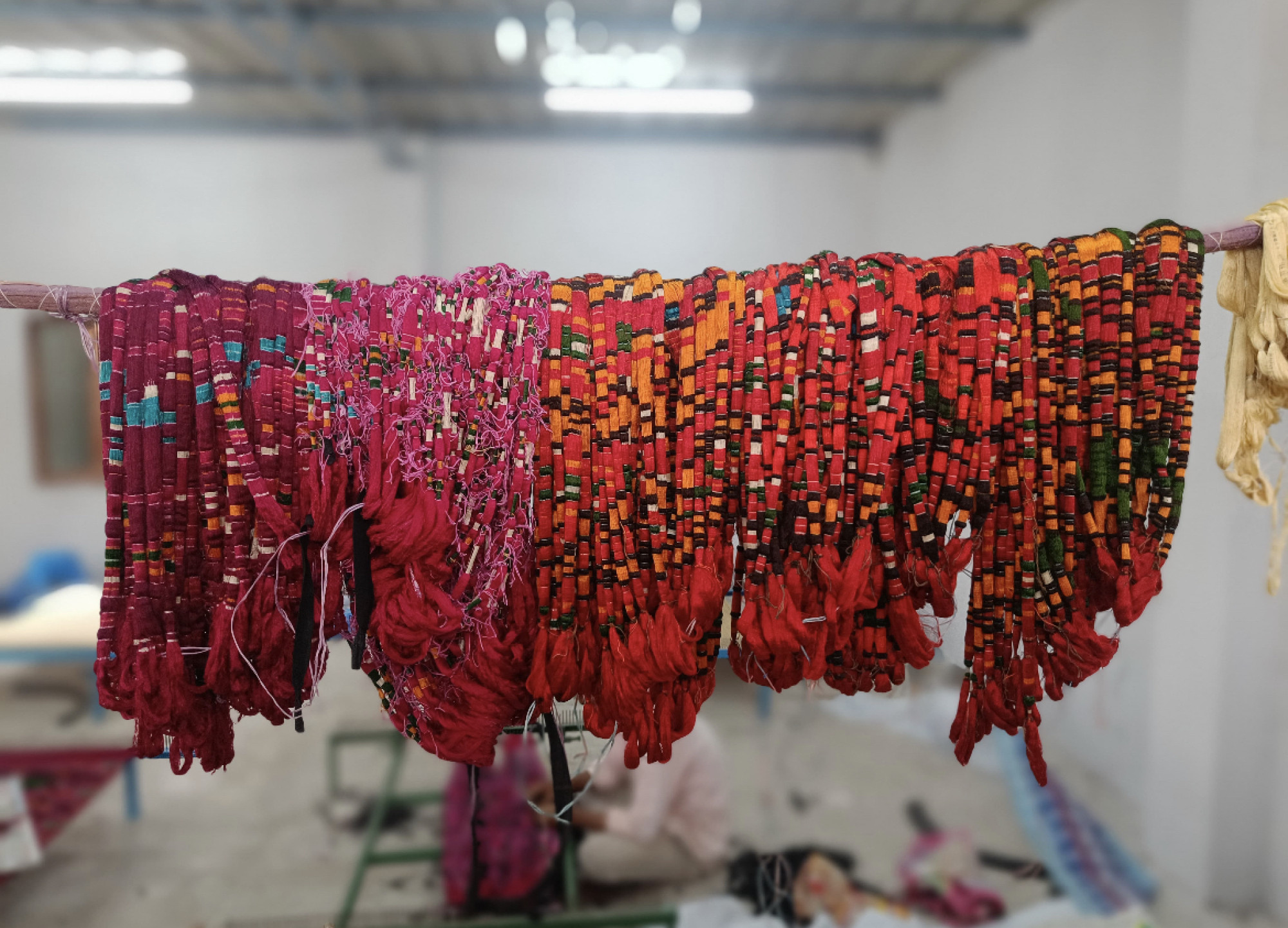
The Pochampally sari is known for geometric designs in rich hues that create a mosaic-like appearance.
“Single ikat is a tie-and-dye method where only the warp is resist-dyed and woven with the weft,” says Bhaskar Saini, who runs the craft village’s Kalaa Punarvi Handlooms – a showroom and two workshops dedicated to producing and selling the Pochampally sari.
“The weaving involves an 18-step sequence; sections of thread tied in an intricate pattern are tied and dyed before that.”
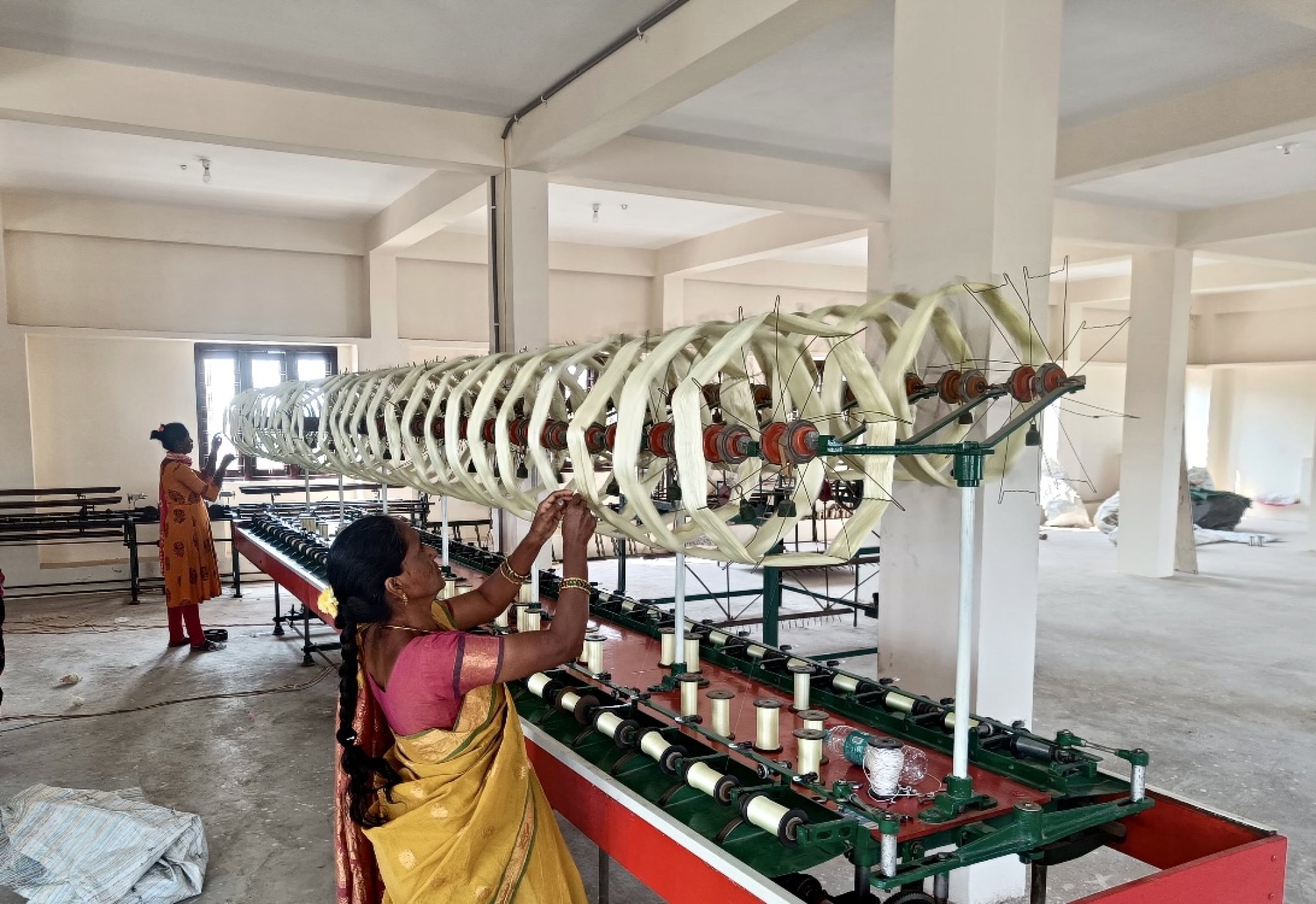
Pure silk is used in various kinds of weave – akshara (a close-knit detailed design), mungi (a plain design) and chepa (a fish pattern) – adds Bharath Saini, Bhaskar’s brother.
For its weaving heritage, Pochampally was handed a Best Tourism Village award by the United Nations World Tourism Organisation in 2021.
Mysore saris feature delicate motifs and are woven using a combination of pure silk and gold zari threads, creating a luxurious and refined fabric
Gaurang Shah
The silk weavers of Kanchipuram are believed by some to be descendants of Sage Markanda, who, according to legend, was the master weaver of the gods. Historians say Kanchipuram – revered by Hindus as one of India’s seven holiest cities – became a silk-weaving centre under the patronage of the Chola dynasty (which was at its peak in the 9th century).
“Two large weaving communities, Devangas and Saligars, relocated to Kanchipuram from Andhra Pradesh and began weaving saris renowned for their rich and lustrous silk, and characterised by vibrant colours and intricate zari work,” says Vinitha Moopanar, of the Kanjeevaram Silk Sarees store, in which top-to-bottom shelving units bulging with rich, lustrous silks in all colours fill two walls.
Known as the “queen of silks”, Kanjeevaram saris are woven in pure mulberry silk and come with both gold and silver zari.

Shah says Kanchipuram weavers “employ the korvai technique, whereby different parts of the sari are woven separately and then interlocked, resulting in a seamless integration of design elements”.
“The designs were inspired by south Indian temples or natural elements like birds and leaves,” says Moopanar. “Popular designs include Rudraksha beads, temples and peacock eye.”
Across in Mysore, the cultural capital of Karnataka state, there’s plenty to see: a 16th century fort; the Mysore Palace, constructed in Indo-Saracenic style and showcasing an ivory and gold throne; and the 17th century Chamundeshwari Temple, home to the patron deity of the Mysore royal family. But no visit is complete without exploring the city’s many silk shops.
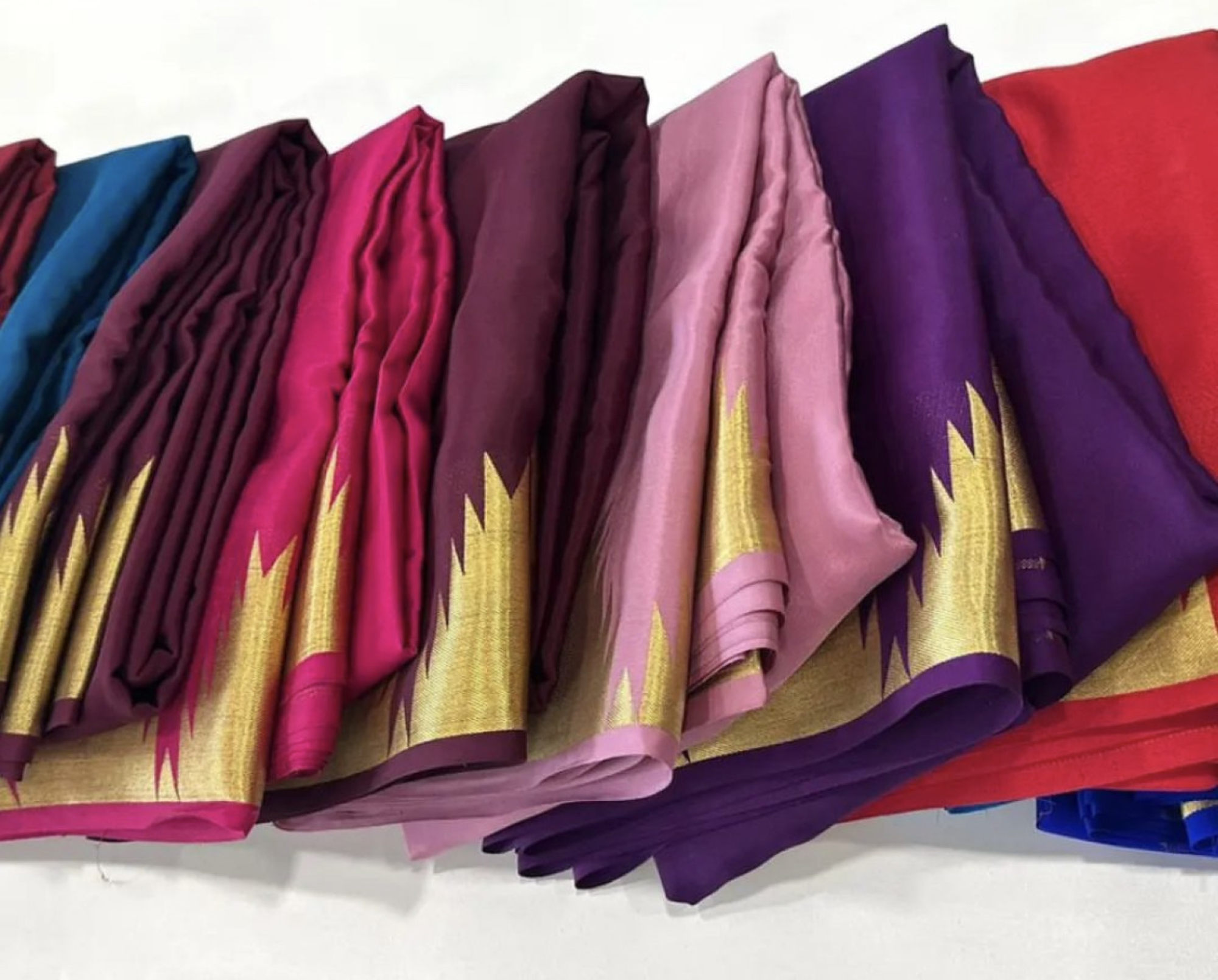
Mysore silk saris, which can be traced back to Tipu Sultan’s reign in the 1790s, are known for their soft texture and minimalistic, elegant designs.
In the early 20th century, the then maharaja, or ruler, of Mysore established a state-run silk-weaving factory to promote the art and provide employment to local weavers. In 1980, the factory was handed over to Karnataka Silk Industries Corporation (KSIC), which continues to manufacture silken masterpieces.
“Mysore saris feature delicate motifs and are woven using a combination of pure silk and gold zari threads, creating a luxurious and refined fabric favoured for its understated sophistication,” Shah says.
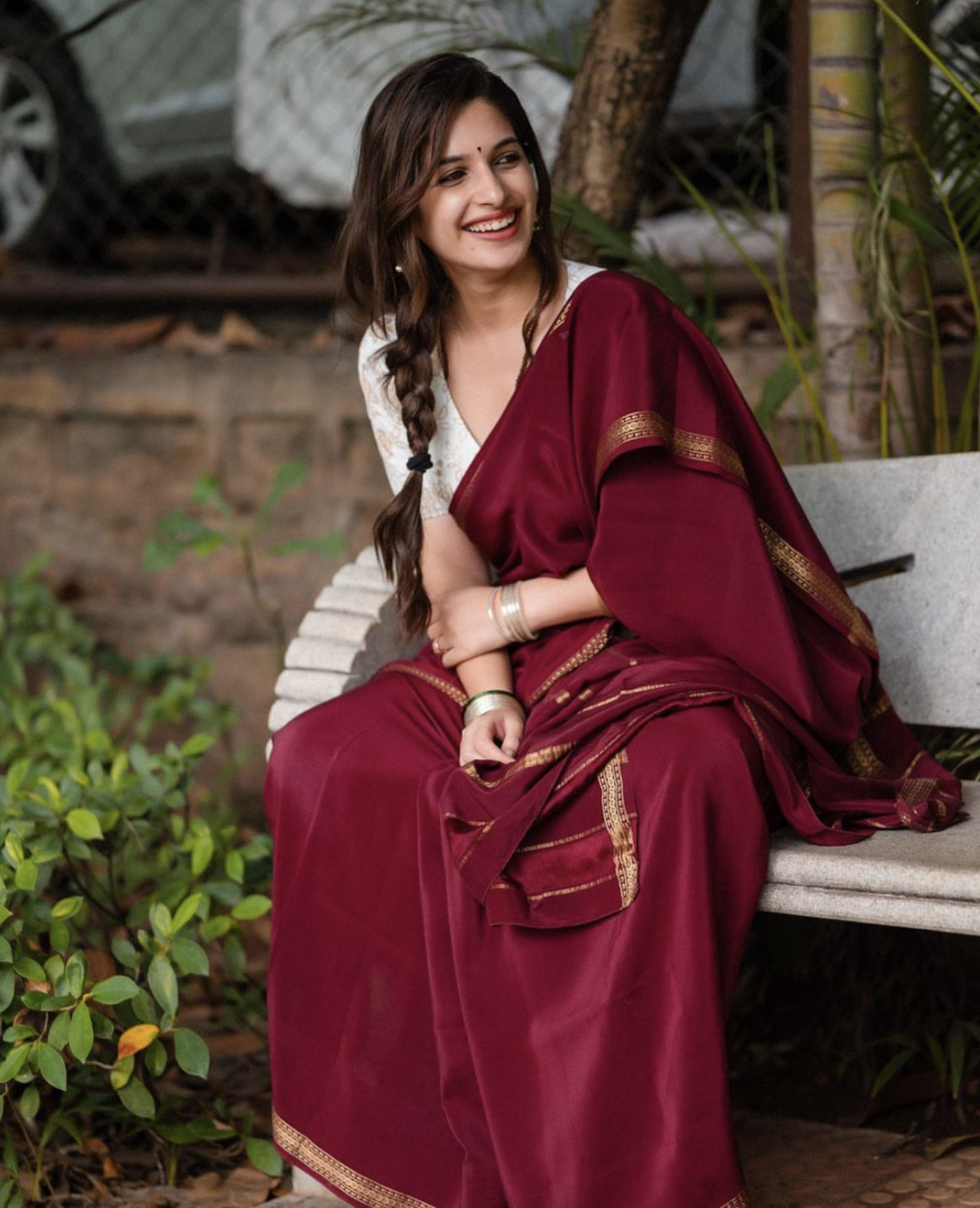
A number of companies offer silk tours in Mysore, but I find that a visit to the KSIC Silk Factory and Showroom, which stands in expansive, tree-lined grounds, serves two purposes: it lets me study the manufacturing process and allows me to buy a shimmering silk sari to take home.
Big vats, large noisy machines and cheerful weavers are all part of the production process. Visitors are often left alone to explore that process – from the soaking and drying of the silk yarn; the winding of it onto bobbins; the steaming of it to smoothen the two-ply yarn; and finally to the weaving of the regal silk. A weaver is never too far away should visitors have questions.
According to Unesco, as an unstitched garment for women, the sari has “no parallels in terms of versatility, richness of colour, texture and variety of weaving techniques using different kinds of yarn, including cotton, silk, gold and silver thread”.
The clusters of weavers across India showcase how motifs, designs and traditions from the past remain unequalled in the present. And all provide stunning statement pieces guaranteed to cause a splash at any lavish Indian wedding.